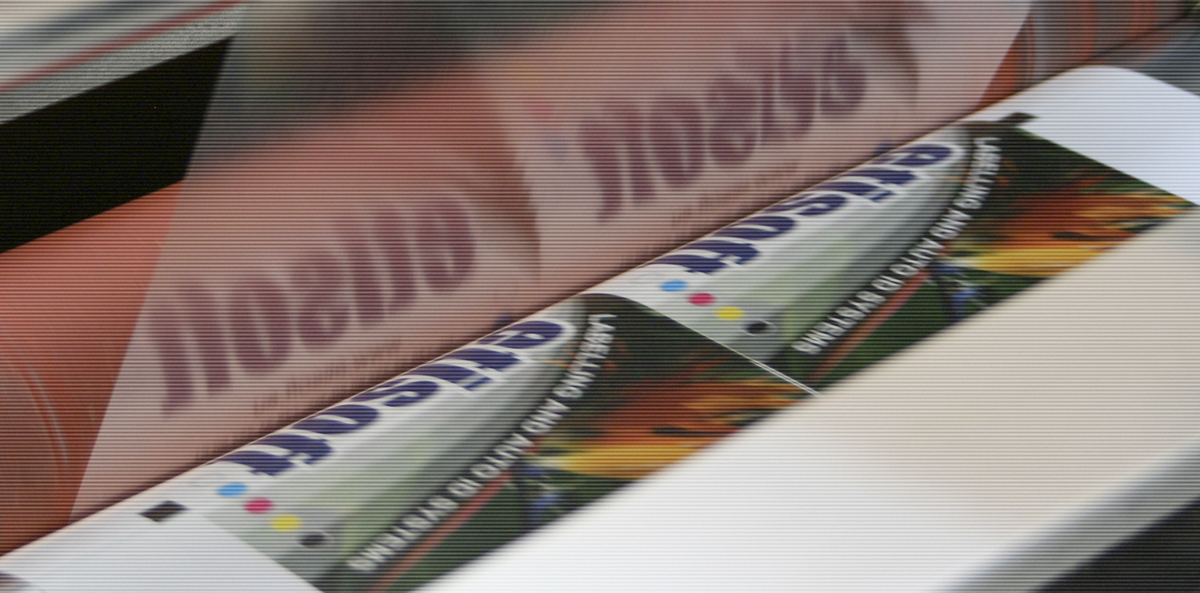
How to secure the print effectively?
Can varnishing and laminating of labels be a guarantee of durability and longevity of the label?
Self-adhesive labels work in very different conditions. They are often exposed to strong dirt, mechanical friction, aggressive substances, weather conditions or UV radiation. That is why it is so important to ask the customer basic questions when choosing a label solution: about the durability of the application, what conditions have to be met by the label and its printing:
- Will the label be exposed to any damage, external factors
- What will the label be applied to, which means – what do we stick to?
- How long should it stay on the labeled product – or how long does it have to last?
If we know that the label will “function in difficult conditions”, then its printing should certainly be durable and resistant to external factors.
So how can we secure the labels?
In the production of printed labels, either flexographic or digital, it is very often necessary to provide additional protection for the printing in order to increase its resistance. Most often two methods are used:
- varnishing
- lamination
What is label varnishing about?
Varnishing is the process of covering all or part of the surface of the label with an additional, transparent layer of paint, which significantly improves its aesthetics. (Depending on the purpose of the label and technological capabilities of the manufacturer, more than one layer of varnish may be applied).
Varnishing can also effectively protect the print against abrasion and blurring in direct contact with water and other more aggressive liquids.
Varnishing is possible only during the production of the label, before the cutting process.
What does self-adhesive label lamination mean?
Laminating – is the process of applying an additional transparent foil to the entire surface of the label, which we want to protect.
Thanks to lamination we can acquire labels of high durability. Laminate guarantees total resistance to blurring, abrasion of the print and significantly increases the mechanical durability of the label.
Properly selected laminate ensures undoubtedly resistance to most chemical substances (oils, greases, petrol, brake fluid, alcohol or toluene).
Benefits of using laminate:
- proper laminate improves the aesthetics of the label:
– glossy surface laminate – increases contrast and colour depth
– a laminate with a matt surface reduces the above. - properly selected laminate improves physical and mechanical properties
Laminate increases the total thickness of the label, which in some applications is strictly defined. In the case of automatic application, the use of laminate increases the stiffness of the material, which makes it easier to peel off the liner - laminate can also be a temporary protective film
In some applications it is necessary to mark the product before the spraying processes (e.g. painting, sandblasting). Such processes certainly make it impossible to read information from the label needed in the subsequent stages of production.
Certainly, in such cases laminate can be used as a temporary form of protection. The laminate should have a suitable adhesive, and the structure of the label must ensure that the laminate can be peeled off without damaging the actual printed label.
When to use laminate protected labels?
Examples of applications where lamination is widely used:
- in the case of permanent marking of goods intended for use for many years (e.g. rating plates)
- to identify models and serial numbers of devices
- to safety warnings and recommendations (e.g. warning labels)
- labels printed by thermal transfer method (e.g. inventory labels)
- laminate as a temporary protective film.
The most popular types of laminates:
- polypropylene film – quite stiff, with high mechanical resistance and limited temperature resistance
- polyester foil – the most commonly used material for label lamination – is characterized by good mechanical resistance, very high resistance to chemicals and temperature. Suitable for outdoor use
- polycarbonate foil – is characterized by the highest mechanical resistance. It gives the label a “technical” look.
To sum up, the selection of an appropriate laminate depends on the conditions in which the label will be functioning and the factors to which it will be exposed. In this matter, customers can fully count on the help and advice of our experts.
(75)