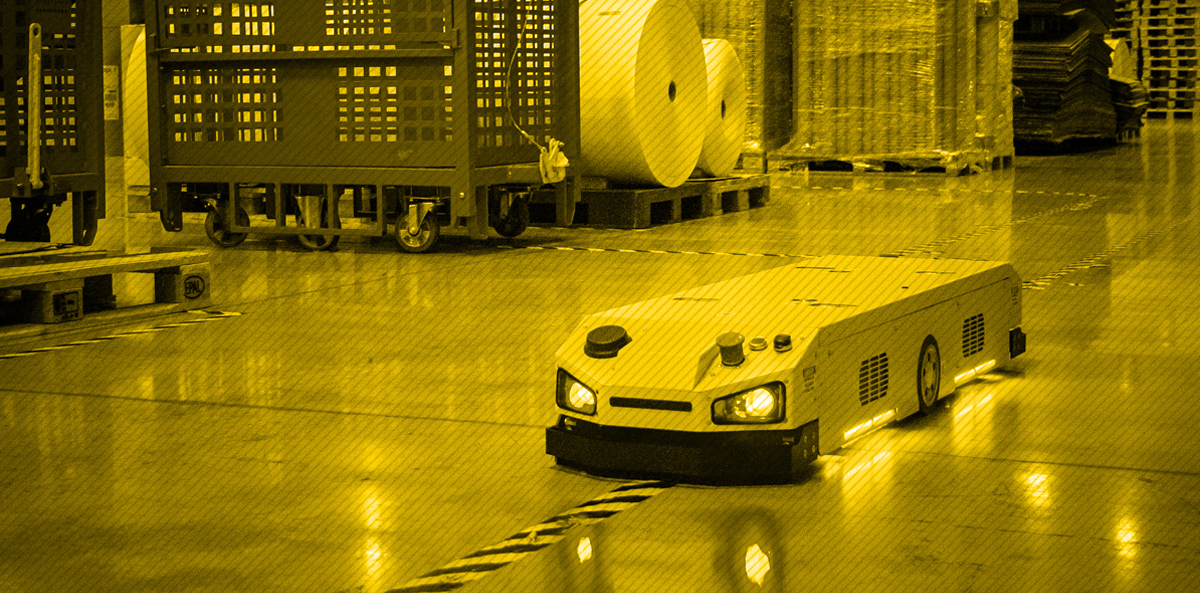
Efficient intralogistics with AGV robots (Automated Guided Vehicle)
Mobile robots: problems and applications
Implementing effective intralogistics without Automated Guided Vehicle (AGV) robots is very difficult, if not impossible. Every day in companies, employees cover many kilometers, moving components needed for production or warehouse operations. This is time-consuming and requires a lot of human resources.
As a result, autonomous transport is slowly becoming a priority for manufacturing companies and related warehouse space.
How AGV robots improve everyday work
The main tasks of mobile AGV robots is transport, which includes:
- picking up and placing goods,
- supply of production and assembly lines,
- storage of products and subassemblies.
In addition, the AGV can be found in laboratories or in hazardous environments. Thus, the purpose of using robots in any form is to replace humans and direct them to more convenient workstations. An unquestionable advantage of AGV systems is their high adaptability and quick reaction to dynamically changing production processes and factory changeovers.
Industry 4.0. – the importance of AGV mobile robots
AGV mobile robots are now at the forefront of technological progress along with autonomous cars, drones and even household appliances. In these areas, there is often a reference to autonomy, that is, independent and internal decision-making. This will of course make life easier. This is why we are witnessing the fourth industrial revolution, the so-called Industry 4.0. One of the most important principles on which modern robotics are based is interoperability, that is, the ability of robots to communicate with each other via the Internet of Things.
In the presented perspective, our company – and in particular Etisoft Smart Solution (a company from the Etisoft Group established to work on new technologies) more than two years ago started to work on mobile robotics. This idea naturally met the needs and problems of our customers, which mainly concerned the shortage of staff and the willingness to develop. As a result of this work, a family of AGV type products called IntraBots was created, which in combination with warehouse and production management systems create Automatic Distribution Systems ADS. The IntraBot family consists of three models:
- IntraBot Pull 500,
- IntraBot Lift 550,
- IntraBot Rail RF
IntraBot Pull 500
The IntraBot Pull 500 is a mobile robot that transports baskets with parts between the warehouse and the assembly lines. The management system collects incoming orders and creates a task for a specific AGV. The vehicle drives up to the basket, hooks it up and starts transporting it to the designated location on the magnetic line. In this way, the risk of supplying the wrong basket with the elements is eliminated and the transport always gets to the right place at the right time.
IntraBot Rail RF
IntraBot Rail RF is a small-sized vehicle that runs on rails mounted under the ceiling. This solution is used in warehouses, where there is a need for constant control of their contents. The Automatic Stocktaking System allows for quick and efficient control of the products in the warehouse. The RFID antenna placed on a moving robot reads the containers with RFiD tags in the warehouse, and the whole operation is performed in just a dozen or so seconds.
IntraBot Lift 550
IntraBot Lift 550 is a type of mobile robot designed to transport loads on standard Euro pallets. The vehicle is equipped with a pallet lifter that picks up and sets down the pallet at the beginning or end of the production or warehouse line. This type of AGV can be navigated by using magnetic tape or laser space scanning.
What is worth noting is the fact that robots work in the environment of employees. Standards in this aspect are very restrictive and no one intends to give them up, because the health of employees is extremely important. Therefore, each robot is equipped with an appropriate class of safety system to ensure safe work in the environment of people.
(1369)