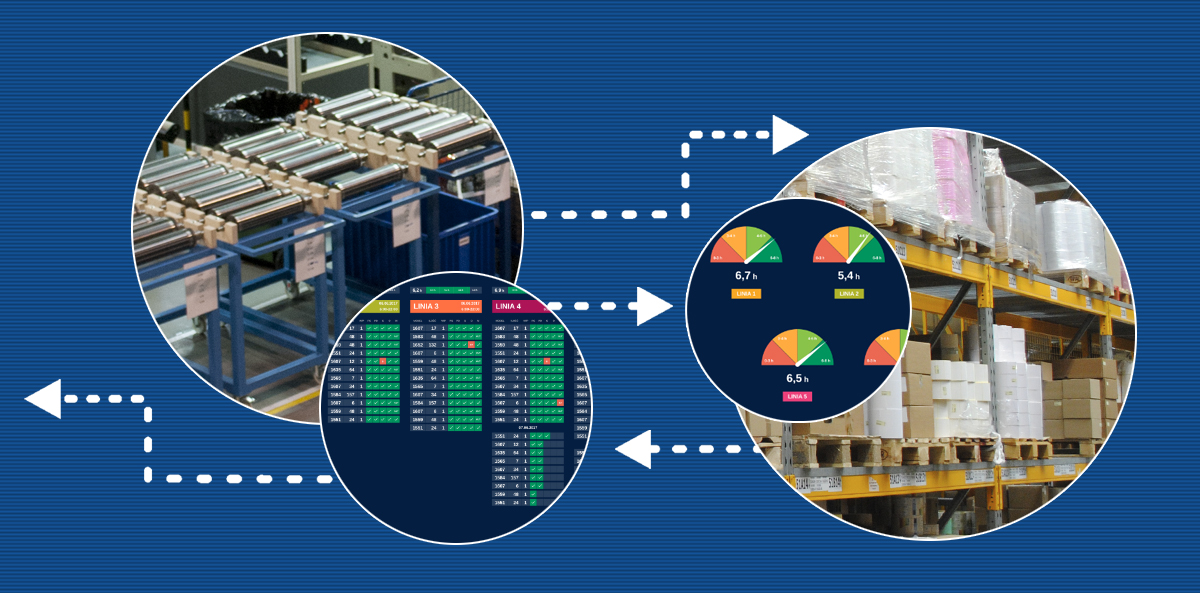
etiSMS – Sequence Management System: a flexible system for every factory
How to simplify and improve communication between warehouse and production operations?
“Sorry, I didn’t notice the email” or “Sorry, I didn’t answer because my phone was muted” – does it sound familiar? Communication means the exchange of information between the participants. Surely data carriers can be words, gestures, texts, images, sounds, electrical signals or radio waves. Basing on the above definition and on the experience of each of us we can get an impression that communication should be characterized by one more term – effective. So, it is necessary to consider whether communication between functional departments in factories is effective and efficient? Certainly, the Sequence Management System created by Etisoft- is helpful. We have implemented it for one of our key customers in the household appliances industry.
It is noteworthy that nowadays, while working, having a computer with e-mail and a phone (smartphone) has become a standard. Especially thanks to the products of well-known IT companies, they have tools for e-mail handling. In addition, more and more other communication tools are available, such as messengers and data exchange tools. Certainly, we can conclude that the availability of communication tools is so large that there is no room for anything else. Is it really so?
Picking components for order processing on assembly lines – how does it work?
It is easy to imagine a production hall with several production lines, a warehouse divided into zones and several functional departments. They pre-process raw materials into components ready for assembly. The processing departments process the raw material into components on the basis of a production schedule. Then, depending on the type of component, the components are transported to the next technological process, which are mechanical assembled in an inseparable or separable form. Components intended for assembly are stored in special zones called buffers. In addition, the assembled components are stored in the buffer zones after the bonding process. In the warehouse, BOMs are selected according to the production orders, which are then the basis for the completion of the picking process. It is worthwhile to notice that the complete sets of components are also transported into the buffer zone. Above all, the information about the readiness of the components is communicated by e-mail or verbally.
Is it possible to communicate on an ongoing basis about the operations described above by e-mail, including e-mail available on the phone? Above all, let’s focus on the effectiveness of such communication. Is it easy to aggregate data from different e-mails sent by different employees for several production orders? First of all, how to make the right decision about starting the execution of this particular production order? Certainly, if you try to answer the above questions, you may come to the conclusion that this is not an easy task.
How does etiSMS visualize the readiness status of components for assembly lines?
First of all, the effectiveness of the etiSMS system is determined by the people who enter the data of component readiness. It seems that a simple panel, where the operator confirms the production of components by stating their number or the completion of components from the warehouse, is an excellent tool to quickly and effectively aggregate the necessary data. The data are being aggregated in relation to the department where they are created and especially in the field of production orders in a way that gives priority to the execution of elementary logistics operations.
In addition, a clear and ergonomic interface for data input minimizes the number of mistakes and, above all, often rotating employees quickly acquire knowledge of the operation. Finally, the collected data, processed and arranged in table form and displayed on a synoptic board above the assembly line, allow easy access to these data. Each line corresponds to a production order and the columns display the order data and component readiness status accordingly. In addition, if synoptic boards are still displayed on the phone, they can be accessed anywhere in the factory. With such an organised data set available, it is immediately clear which production order can be started for processing. The decision can be made on the fly, without delay.
Above all, etiSMS is used to communicate the execution of warehouse and production operations, so that the readiness status of components is visualized at the assembly lines. That’s why it’s easy to make decisions about starting up a production order. The system consists of three components. The first one is the dispatcher – a management module with a database, where the production schedule is entered and information about the readiness of components is reported. The second one is a terminal (interactive synoptic board), which enables registering the activities carried out. The third element is a synoptic board, displaying component readiness statuses.
The structure of the system is presented in the following diagram. (The above system has been prepared for the customer’s needs in the Polish language version. However, there is a possibility of its modification)
Terminal and synoptic boards: functions, benefits
The terminal allows to record data about the production of components and has three basic functions:
- presentation of schedules for assembly lines with information about which component is needed and in which quantity
- presentation of the work progress of the currently executed production on the assembly line
- reporting on the preparation of parts for a specific line.
Any number of terminals can be located in the factory.
A synoptic board displays the information collected by the terminals. The four basic functions of the board are presenting:
- the status of the preparation of parts on the individual exhausts
- the currently manufactured component on the assembly line
- an approved production schedule on the assembly line
- the amount to be done, the time when the job starts
Due to the fact that the synoptic board is created in web technology, it can be displayed on any device (including smartphones) that allows you to browse the web. This system architecture allows data to be displayed anywhere on the factory site. Placing the boards over the assembly lines allows you to inspect the state of production while keeping an eye on the assembly line.
The system is also complemented by a warehouse component. This is the most complex element of the etiSMS system.
The structure of the warehouse component is presented below.(The above system has been prepared for the customer’s needs in the Polish language version. However, there is a possibility of its modification)
Picking in the warehouse zone – the last element of the Sequence Management System
The main screen of the terminal for the recording of completed components in the warehouse is no different from the ones located in the technological departments. As a result, by selecting a production order, the operator moves to the next screen. Confirmations for the collection of components from different warehouse zones are reported here. Finally, the warehouse module has a synoptic board. Above all, it shows the current state of preparation of the components at the time. Certainly, thanks to this data presentation, the warehouse operators can prioritise their activities at the operational level.
Finally, the last element that can be used to expand the etiSMS system for the warehouse is the synoptic board. It shows a summary of the picking process in the warehouse area. Above all, this summary shows where the shortages are in a different way. First of all, for those who manage the picking process at the operational level, this is an indication which tasks should be treated as a priority.
The appearance of the board is presented below.
etiSMS, a flexible system
Most noteworthy is the fact that the etiSMS system allows for a significant simplification and improvement of the communication between the production departments, the warehouse and the assembly lines. Above all, aggregating information in an ergonomic way and presenting it in a way that is attractive to the receiver is an advantage of the solution. Certainly, the solution to the problem of effective communication between the areas of the organization can be implemented thanks to simple tools and technologies with a high level of development. As a result, the failure rate is minimised, which directly leads to tool availability. The flexibility of the etiSMS system allows it to be implemented in almost any factory, which makes the solution valuable.
If you are interested in our offer, please contact us.
*The above system has been prepared for the customer’s needs in the Polish language version. However, there is a possibility of its modification.
(133)