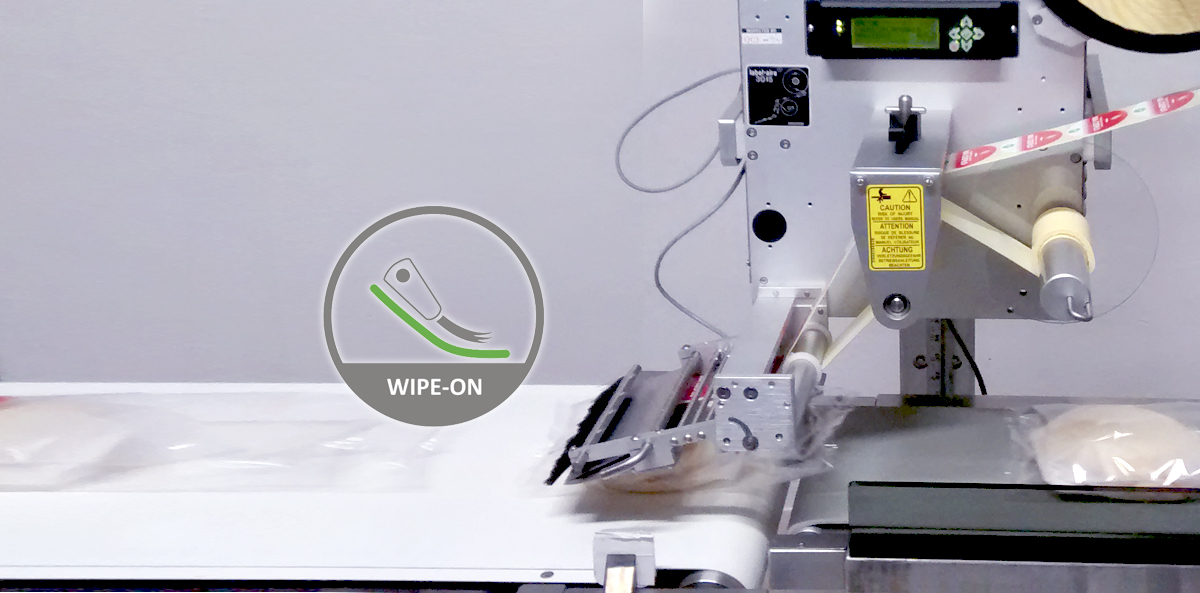
Etisoft’s solution increased production efficiency by half
Labelling systems for deep frozen products
Deli food producer (roasted sandwiches, tortillas) for chain service points – one of our customers – turned to Etisoft with a demand for automatic label application solution for its products. Our visit on the production site which aimed at a detailed analysis of customer needs and site conditions allowed us to prepare an accurate solution.
Fantasy Food (Kobyłka, Poland) is a family company with 26-year-old presence on the market, producing frozen deli mainly for gas stations and chain stores in Poland and Europe. Before Etisoft installed its device, the labels were applied to products manually during production process. Unfortunately, due to a significant pace of production line, it occurred from time to time that the operator failed to label all items. It resulted in a necessity to sort products manually before they were put into the packages in order to pick out deficiencies. The manual application system used so far introduced confusion and lack of reproducibility in the final stage of the production.
Increasing production and growing number of orders forced us to find areas where we could enhance efficiency, while staff could be directed to other activities and employment rate wouldn’t have to be increased. One of such areas was a final stage of applying labels to ready goods. Demand for labelling every product during full production load put human presence in this process into question. Replacing human with a machine seemed like a best solution – says Jarosław Hubert from Fantasy Food Sp z o.o.
With pneumatics and blow?
Our customer required real-life tests on a production life with a demo device. Accordingly to our expectations, the applicator managed to apply the label on each item in a correct manner. The positive test results assured our customer that implementation of application device is indeed reasonable and the staff had an opportunity to get to know it and see how simple to use it is.
A transport line speed of 20 m / min and a typical product shapes (unique height) contributed to a decision to apply the Label-Aire basic linear applicator. Model 3015-ND, which is a very simple applicator for regulation and operation, but at the same time has advanced customizable features, perfectly suited the needs and expectations of the client. Products placed in plastic bags filled with air, suggested the use of a pneumatic device with a feature enabling blowing on the label. Such a solution is expensive and also requires supply of compressed air from the compressor of adequate output voltage. Our alternative to the more expensive solution was a wipe on application and this type of applicator was proposed in this solution.
Easy recall of the parameters
Our customers’ biggest concerns related to the proper operation of the applicator with non-standard shapes of labels, such as circles, triangles etc. Calibration of the applicator into any shape labels and the simultaneous setting stored in the memory of the device enabled easy recall of the necessary parameters from the operator, depending on the intended shapes of labels. For the fixed line speed, and the location of the labels on the product, regardless of its type, the control range was brought to an absolute minimum. Due to the different heights of products depending on the assortment, a manual change of the suspension height of the applicator before starting the production was necessary. This problem was solved by installing additional joint stand.
The expected date of installation of the ordered applicator and stand brought no surprises, and the end result was aligned with the effects obtained during testing.
(145)