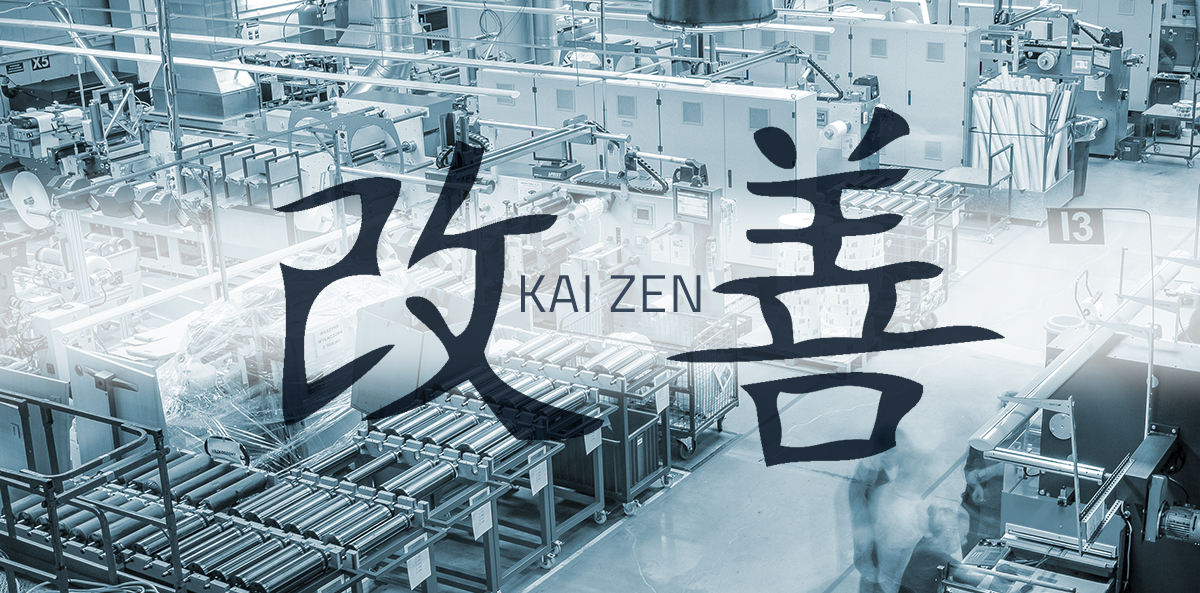
How the kaizens of our employees improve everyday work in Etisoft
From idea to implementation
In the Etisoft, we involve and encourage employees to propose rationalisation ideas – kaizens. Since July 2017, when we implemented the Lean Management policy, our employees have proposed over 470 applications, which means 26 each month! The record holder has 38 of them in his account! We boast about it, because each of our employees has the opportunity to change their workplace and the environment in which they work for the better thanks to kaizen.
So far, employees of the Operations Division have shared their ideas for improvement of work. From February this possibility, after managers’ training, will be available to other employees of the company.
Minor improvements that do not require large financial outlays support our work in the following categories:
- ergonomics of work and savings,
- technologies
- health and safety
innovation.
We are also tabling amendments in the category of ‘a well-known problem’.
Kaizens help us to eliminate waste
Kaizens are an element of Lean culture, and Lean Management is a democratic system, because it involves listening to the voice of employees. They are the ones who work on machines, organize shipments, place orders and know best what to do to avoid wasting time and money. In the Etisoft, all ideas are discussed by the committee. After analysing the applications, it is the commission that decides about their future development. The most interesting and those that can realistically improve our processes are implemented. So far, we have implemented 64% of the submitted applications. The average implementation time is 62 days. It is due to the fact that some applications require many organizational changes or purchase, or building tools that are difficult to access.
Ideas submitted to us are both proposals that do not require much money or great “revolutions”, as well as ideas that change the adopted work standards, or that require the purchase of additional equipment. We also have rationalisation ideas from our employees, which require contact with machine manufacturers. Many times this means that the time that has to pass from idea to implementation has to be extended – explains Tomasz Machnio, Lean Coordinator in our company.
Kaizen in our practice
How do employees’ kaizens help us in our daily work? Here are a few implementations that have significantly improved our daily activities:
- One of our colleagues used his IT passion and created a script that automatically browses through forecasts from customers. Previously, the Customer Service team spent about 2 hours a week analysing them. After the implementation of the proposed solution, it takes about 5 minutes.
- When disassembling tools from the machine, operators sometimes mistakenly put them into the wrong boxes, mixing the sets at the same time. Completing the right set after such a mistake took even several minutes. The author of this kaizen suggested that all elements of a given set should be marked in one color so that it is easy to complete them when disassembling. Thanks to this, it was possible to practically eliminate mistakes in 100%, which automatically saved the operator’s time.
- Forklift operators pointed to poor visibility when moving with a forklift truck in one part of the warehouse. Employee safety and limiting the risk of company property were minimized by installing a safety mirror at the request of the author of the kaizen.
Other Lean Management tools that we use are: „5S” (a well-ordered and organized workplace) and SMED – a collection of techniques which shortens the time of machine changeovers. Both rules are successively implemented and developed in etisoft.
(116)