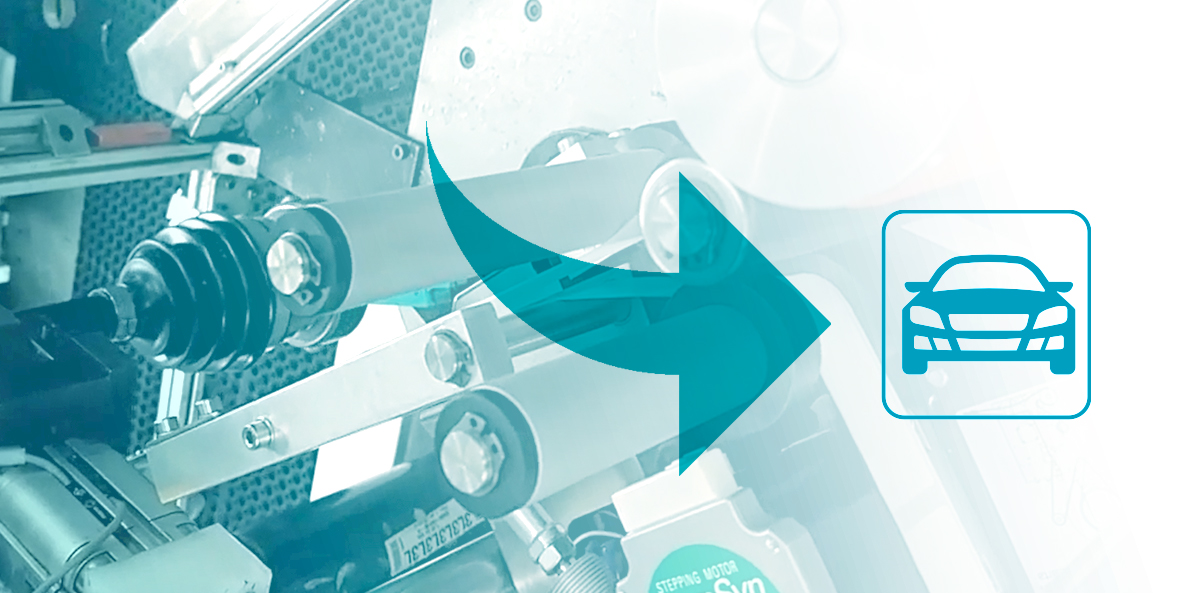
Marking of car axles in the production process
Automatic application of labels on components in the automotive industry
The marking and later identification of a component in the automotive industry is a key process of tracking and verifying the correctness of assembly of components and subassemblies in a car.
Our customer, a supplier of car axles, is obliged to mark each of its products. Marking it with: reference number and other data. They are needed for identification and registration during production and at the final stage in the assembly line.
First of all, due to the shape of the product and the nature of the manufacturing process, the axles are marked with a label on the circumference of the steel shaft. Earlier, the labels are printed on a thermal transfer printer. The properties of the consumables used (label and ribbon) allow them to be used in difficult external conditions. First of all, they guarantee resistance to oil, temperature and abrasion.
Small space determined the use of the smallest applicator
The character of production, which consists of passing the half-axes to the next assembly stations, is certainly not advantageous for manual application of the label. First of all, the need for operators to wear gloves does not help. Therefore, the customer decided to automate the process. That is why he used one of the production modules to implement a half-axis label applicator in it. The free space available in a built-in assembly station determined the use of the smallest applicator from our offer. The basic model of the ASE DS100 linear applicator (wipe on/merge) met the requirements set for us. It has an extended guide ended with a blade separating the label from the liner. In addition, it also has a pneumatic system that brings the blade closer at the time of application.
The application of the label is followed by an extension of the actuator. It is activated by a PLC that manages the production station. Finally, the small roll, mounted at the end of the peel-off edge, causes the appropriate pressure. The result is a perfect adhesion of the label to the surface of the product. It is noteworthy that the speed of the label feed corresponds to the speed of rotation of the half-axis.
The implementation we proposed solved the customer’s problem. The final effect was achieved thanks to the small size of the ASE DS100 applicator, which has its power supply module in a separate electrical box mounted at the required distance from the place of installation of the label applicator.
Finally, we have improved the customer’s production operations, eliminating the need for operators to participate in the product marking process.
If you want to learn more about this and our other solutions for automatic label application, please contact us.
(142)