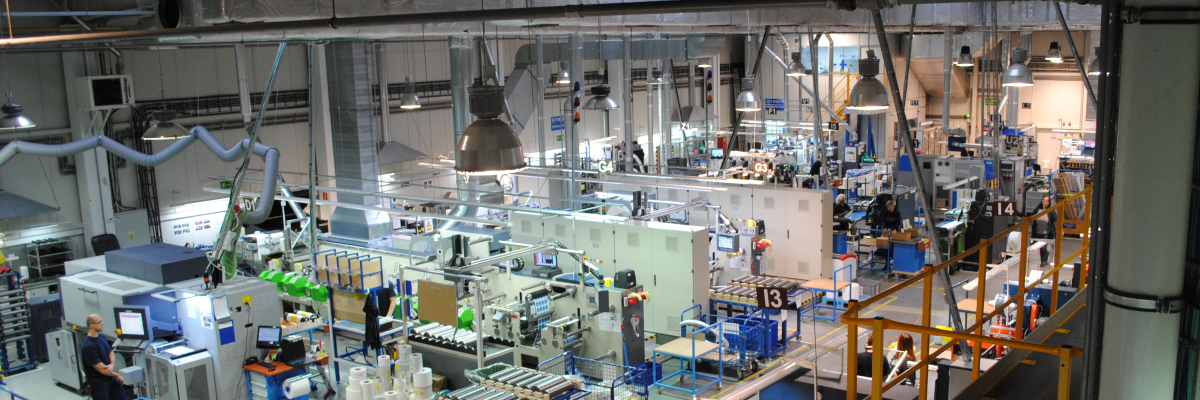
Gidue Master M5
Modern production machines
In order to meet growing demands of our customers, we decided to grow and renew our machine park. We chose to buy Gidue Master M5 – six- and eight-colour flexography machines.
Gidue Master M5 features
Their characteristic feature is the ability to print the maximum band width to 375 mm, which classifies them as a medium-band machine. Master M5 devices replaced the previously used older models. Master M5 is the most technologically advanced models of the Gidue machines. Thanks to its technical parameters they allow to print high-precision, complex and specialized labels. Choosing the right materials, paint and tools, this machine provides repeatable print, which is the basis for flexographic printing.
Labels printed on Gidue Master M5 can be subjected to a full range of finishing options, including e.g. print protection by lamination. Other possibilities of the machine, include double-sided printing, or printing on the adhesive. Fully automatic control of all the print variables and finishing options allows to print labels with even better quality. It is worth underlining that system for polymers auto-match is very important for any printing option with up to eight colors. Very sensitive cameras installed on the machine are able to detect even the smallest deviation of color matching. The machine itself keeps the match and corrects it. Automation of rollers fitting is translating into significant, up to 50 percent savings on the raw material on “pre-run” stage of the machine. Servo motor on each of the rollers makes them possible to be operated independently – if we match colors with one another, the printing section engine speeds up or slows down. Printing with water and UV inks makes Etisoft offer more attractive and enables us to meet the high demands of our customers, providing much better print quality and its longer service life. One of the biggest advantages of printing with UV inks is its durability. On the other hand, the decision to use water-based paints results from customer requirements, e.g. later thermo transfer overprint.
Is this the right choice?
Using new machines and new features in the daily work made it possible to reduce the changeover time – estimated at up to 50%, reducing the amount of raw materials consumed in the so-called “pre-running” phase. Using servo in M5 machines made it possible to double the production of labels.
What is important is that the production of labels on M5 machines does not rely only on our technology – also on the most experienced operators in our company.
(245)