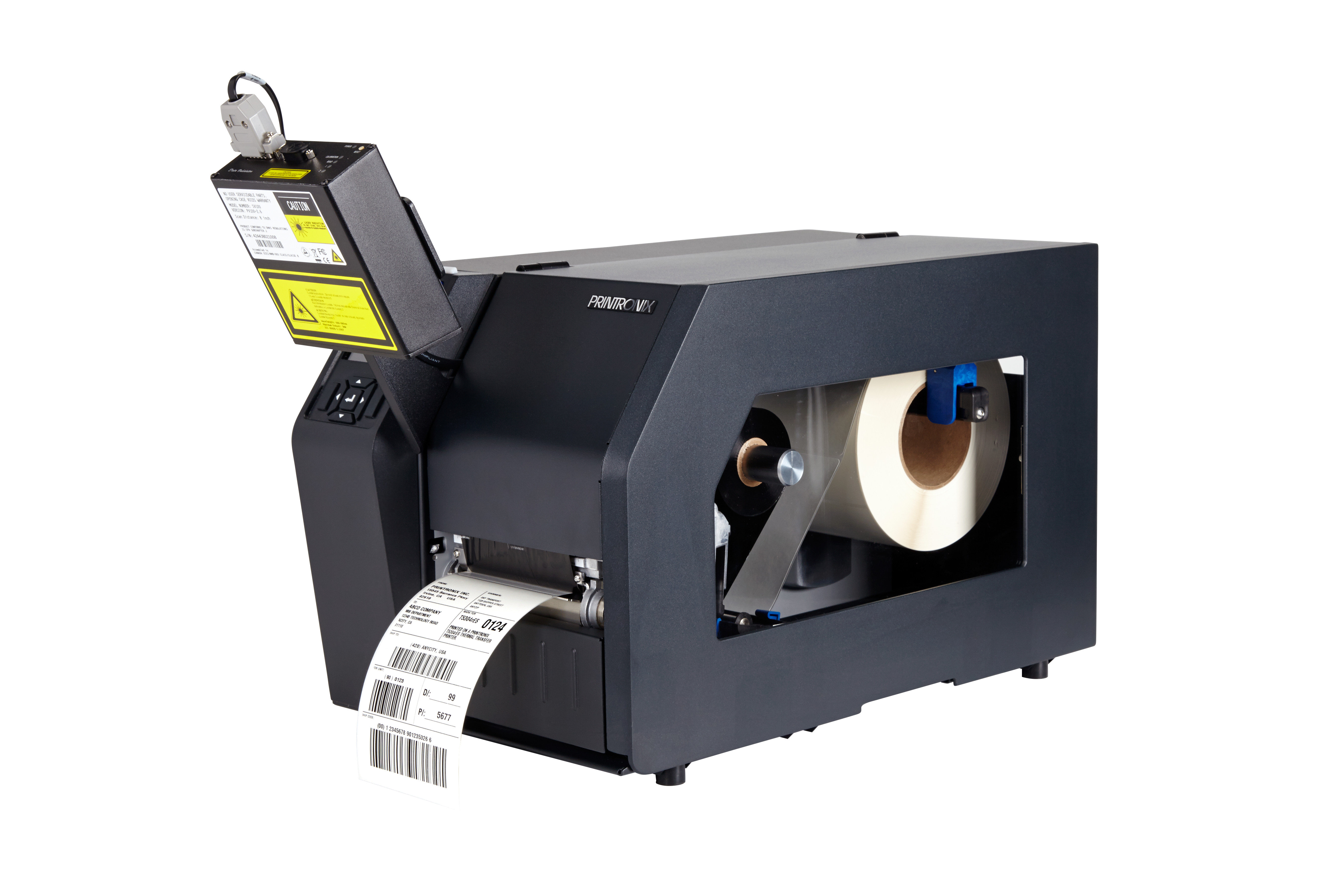
Thule – codes verification system
Barcodes, can anything go wrong here?
We assumed it will be safest to check if barcodes are correct the moment they are printed.
The printers we used so far, were not able to verify if printed barcodes are correct in terms of quality.
Barcodes
Barcodes. We all know them. Not everyone knows what they mean or where to use them, but we cannot imagine doing business without them. They are everywhere.
We see them on daily usage products, at shops, warehouses, laboratories, tickets or ads… We use them on production lines, warehouse management and transport. They make it easier to manage goods and products, improve logistics processes, eliminate mistakes and make work faster.
Barcodes, legibility first
As a rule, thy have only advantages, and that’s true. Until they work. Until they are legible, to be precise. Unfortunately we meet some obstacles here. Despite high class printers, properly selected consumables, well trained staff we can see barcodes that are printed incorrectly. What then? If you work in a store, you will write product’s value directly under the barcode.
Automatic systems
We don’t have time for that when it comes to advanced systems. We don’t even have possibility in some cases. Barcodes are read automatically by scanning systems and error or no reading at all causes problems. Sometimes it means longer time for goods admission or delivery and sometimes it means the production line will be stopped. It is a cost. Everytime. If that takes place at our customer, then we lose not only time and money, but also our reputation which may lead to financial penalty or even contract breach.
Companies all over the world face such challenges and it does not matter if you are small or global. Also Thule, Swedish leader in production of roof racks, sports carriers for bikes, ski, canoes, child carriers and car seats or travel bags, etc.; was urged to find some solution to this problem.
Even though Thule is well aware of product marking and did their best to deliver their products with correct barcodes, they also encountered some problems in this area. Wanting to reduce risk of mistakes, Polish branch of Thule turned to Etisoft asking for help in finding solution that would provide effective verification of already printed barcodes.
Early verification of barcodes
We assumed it will be best to check if barcodes are correct the moment they are printed. The printers we used so far, were not able to verify if printed barcodes are correct in terms of quality.
Visual verification, done by staff would be time consuming and would not give 100% guarantee. Some barcodes look perfectly normal, but the they turn out to be incorrect, not compliant with quality criteria and hence, illegible.
Also fixing standard readers on printers wasn’t good enough. The system made it possible to read barcodes and potentially stop printing or reprinting in case of an error, but, due to certain expectations of our customer, it still wasn’t what Thule looked for.
Printer with dedicated system for barcodes validation
Another idea was to install printer with dedicated system for barcodes validation. And that was it! Each printed barcode is automatically verified not only in terms of its legibility, but also ISO compliance (i.e. proper contrast, margins). In case of erroneous reading, system administrator may define various actions such as rescanning, print stoppage or reprint. All those actions can be combined. There is no worry that such an erroneous label will be back in circulation – it is being destroyed by printing selected pattern on – such as checker, for instance.
In case next few labels are faulty, which may be caused by e.g. head damage, print process is stopped by the system which signals the problem not only by showing big and visible communicate on printer’s monitor, but also by audio and visual signaling.
Codes verification system – implementation
It didn’t mean just installing the printers. It was necessary to adjust to limitations forced by the system Thule used. It was pretty challenging to generate labels by server located abroad and hence with no possibility to interfere into print patterns in any way. Also, number of formats and materials used for printing labels was such a limitation.
Yet, thanks to great engagement of labeling staff and IT department support, we managed to run numerous tests. Eventually, the system was configured in such a way so as not only to print and verify labels correctly, but also to require as little interference from operators as possible. This implementation not only improved marking quality, but also made every day work easier.
Janusz Dembowski, Thule Sp. z o.o IT manager:
Before we installed printers offered by Etisoft we encountered multiple inconveniences due to erroneous barcode print. We had to bear additional cost connected with goods delivery, repacking, remarking and following shipment. Since we implemented this system, not even one claim occurred. Also handling the printer itself makes no problem. Actually the only time we focus on it is when we want to show off how our barcode verification system works. As a result, all our barcodes are verified and only the correct ones are being used for production purposes.
(231)